In the field of modern manufacturing, the integration of advanced technologies has greatly changed the production process. One of these revolutionary innovations is Automatic Grinders, which redefine precision, efficiency and consistency in manufacturing.
Automatic Grinders are precision machines equipped with automated controls and precision engineering designed to grind and shape a variety of materials with precision and repeatability. These machines play a key role in various manufacturing sectors from automotive and aerospace to tool and mold making, providing countless benefits and reshaping the manufacturing landscape.
The main advantage of Automatic Grinders is their ability to provide precise and consistent results. Using advanced computer numerical control (CNC) systems and programmable logic controllers (PLC), automated grinders can perform complex grinding operations with micron-level precision, ensuring uniformity and adhering to tight tolerances. This level of accuracy is critical in an industry where part quality and dimensional accuracy are critical.
Automatic Grinders help increase productivity and cost-effectiveness. By automating the grinding process, these machines can operate continuously, minimizing downtime, maximizing output and streamlining production cycles. This means shorter lead times, lower unit costs and improved resource utilization, ultimately making manufacturing operations more competitive.
The integration of automation in the grinding process can also improve workplace safety and ergonomic benefits. Since manual grinding operations are physically demanding and potentially hazardous, Automatic Grinders mitigate risks associated with repetitive tasks, dust exposure and operator fatigue. This not only creates a safer working environment, but also promotes employee well-being and efficiency.
Automatic Grinders seamlessly machine complex geometries and difficult-to-machine materials. Whether producing complex surface profiles, precision molds or high-performance parts, these versatile machines can handle a variety of materials, including metals, ceramics and composites, while maintaining superior surface finish and geometric accuracy.
As Industry 4.0 technologies continue to evolve, Automatic Grinders are being integrated with smart features such as real-time monitoring, predictive maintenance systems and data-driven analytics. This connection enables proactive maintenance, process optimization and adaptive control, further improving the operational efficiency and reliability of automated grinding systems.
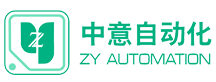